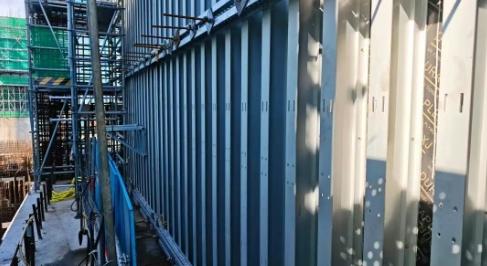
陸豐核電1、2號(hào)機(jī)組核島的輔助廠房和附屬?gòu)S房墻體尺寸大,覆蓋面積廣,在廠房墻體混凝土澆筑中,傳統(tǒng)的常規(guī)大模板存在諸多局限性,主要有四大痛點(diǎn):
未設(shè)置起重吊點(diǎn),吊裝困難且不安全。
未設(shè)置加固平臺(tái),模板加固需配合腳手架平臺(tái),投入人工較多且工序復(fù)雜。
拉桿數(shù)量多,增加預(yù)埋拉桿孔的同時(shí),也增加了材料用量,增加施工成本。
面積較小,對(duì)于大方量混凝土投入模板量及人工較多。
為將陸豐核電項(xiàng)目打造成為精品工程、標(biāo)桿工程,項(xiàng)目管理團(tuán)隊(duì)深入踐行“嚴(yán)慎細(xì)實(shí)”工作作風(fēng),大力弘揚(yáng)“陸核精神”,堅(jiān)持“三個(gè)圍繞”價(jià)值導(dǎo)向,分機(jī)組、分領(lǐng)域、分層級(jí)持續(xù)推進(jìn)“五化”建設(shè)走深走實(shí)。按照“應(yīng)模盡模、能模盡模、宜模則模、未模創(chuàng)模”原則,項(xiàng)目管理團(tuán)隊(duì)聯(lián)合上海核工院、中核二二陸豐核電項(xiàng)目部,在前序項(xiàng)目8大類(lèi)26項(xiàng)模塊化施工經(jīng)驗(yàn)的基礎(chǔ)上持續(xù)開(kāi)展模塊化。此次投入使用的直行墻大模板正是施工工藝模塊化建設(shè)內(nèi)容之一。相較于常規(guī)大模板,直行墻大模板具有安全性、經(jīng)濟(jì)性和實(shí)用性三大優(yōu)勢(shì)。
01安全性設(shè)計(jì)與加固措施方面
直行墻大模板通過(guò)多維度優(yōu)化確保施工安全可靠。模板增設(shè)經(jīng)結(jié)構(gòu)強(qiáng)度、材料性能及防滑設(shè)計(jì)專(zhuān)項(xiàng)優(yōu)化的專(zhuān)業(yè)起重吊裝吊鉤,可安全承載模板重量,實(shí)現(xiàn)穩(wěn)定起吊與懸掛,降低吊裝隱患。加固采用M17高強(qiáng)拉桿自下而上進(jìn)行,先在地面完成第一層、第二層高強(qiáng)拉桿安裝固定,再于模板結(jié)構(gòu)上架設(shè)三角掛凳,并通過(guò)螺栓將折疊平臺(tái)與大模板體系牢固連接。模板頂口與底口配備集成裝置增強(qiáng)整體性,底部三角架開(kāi)設(shè)直徑22mm孔洞并焊接M20螺母,與斜撐銷(xiāo)軸精準(zhǔn)連接固定,提升整體穩(wěn)定性。此外,大模板重復(fù)使用率高,能顯著降低材料損耗與人工成本,同時(shí)配套完善的安全防護(hù)措施與穩(wěn)固支撐體系,可有效規(guī)避模板拆除過(guò)程中的安全事故,確保拆除作業(yè)安全有序開(kāi)展。
02經(jīng)濟(jì)性方面
陸豐核電1、2機(jī)組應(yīng)用的4880*5800*18規(guī)格大模板體系優(yōu)勢(shì)顯著。該體系憑借標(biāo)準(zhǔn)化大尺寸設(shè)計(jì),大幅壓縮材料拼裝耗時(shí)達(dá)50%,有效提升施工效率;同時(shí),其良好的整體性減少了生產(chǎn)過(guò)程中的材料損耗,實(shí)現(xiàn)施工成本的降低。在龍骨與支撐結(jié)構(gòu)設(shè)計(jì)上,大模板橫向配置3道雙14槽鋼龍骨,豎向采用間距300的H20鋁工字梁。經(jīng)嚴(yán)謹(jǐn)力學(xué)計(jì)算驗(yàn)證,3道雙14槽鋼龍骨即可滿足受力需求,相比傳統(tǒng)方案有效減少槽鋼用量,簡(jiǎn)化拼裝流程;而H20鋁工字梁的應(yīng)用,不僅增強(qiáng)了大模板體系的安全性,更顯著提升其整體剛度與穩(wěn)定性,在保障工程質(zhì)量的同時(shí),實(shí)現(xiàn)了材料成本與施工難度的雙重優(yōu)化。
03實(shí)用性方面
大模板憑借精密的支撐與緊固系統(tǒng),可高效抵御新澆混凝土產(chǎn)生的側(cè)壓力,顯著降低模板變形、鼓脹風(fēng)險(xiǎn)。相較于小塊散拼模板,大模板大幅減少接縫數(shù)量,經(jīng)特殊設(shè)計(jì)與處理后,能有效防止漏漿問(wèn)題,確保澆筑出的混凝土墻面平整光潔,完全契合核電工程對(duì)高品質(zhì)混凝土外觀的嚴(yán)苛標(biāo)準(zhǔn)。在項(xiàng)目施工過(guò)程中,少拉桿設(shè)計(jì)大幅縮短施工周期;上部操作平臺(tái)的創(chuàng)新設(shè)置,既減少了腳手架搭設(shè)量,又避免了交叉作業(yè)干擾,顯著提升結(jié)構(gòu)施工質(zhì)量、精度與效率,同步強(qiáng)化作業(yè)安全性,為混凝土振搗作業(yè)提供了便捷、高效的操作空間。
在編制施工方案階段,陸豐核電項(xiàng)目管理團(tuán)隊(duì)便對(duì)現(xiàn)場(chǎng)大模板支設(shè)工況進(jìn)行深度調(diào)研與系統(tǒng)性規(guī)劃。通過(guò)精準(zhǔn)設(shè)計(jì)與精細(xì)化制造流程,定制的直行墻大模板在生產(chǎn)環(huán)節(jié)實(shí)現(xiàn)了高度一致性與施工精度保障。此外,大模板系統(tǒng)依托標(biāo)準(zhǔn)化、模塊化設(shè)計(jì)理念,顯著簡(jiǎn)化了施工過(guò)程中的組織管理與多方協(xié)調(diào)工作,不僅大幅提升項(xiàng)目管理效能、有效縮短施工周期,還通過(guò)優(yōu)化資源配置降低了綜合成本,實(shí)現(xiàn)施工效率與經(jīng)濟(jì)效益的雙重提升。